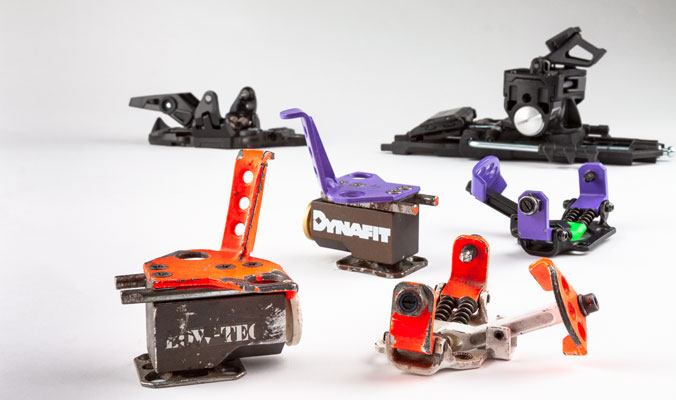
In 1982, 12 years before the birth of Backcountry Magazine, Austrian mechanical engineering student Fritz Barthel and his partner decided to tack the summit of Mont Blanc onto the end of an April climbing trip. Burdened by heavy gear and 200 cm slalom skis, they were exhausted by the time they reached the summit. That climb instilled Barthel’s drive to design lighter gear.
Fritz Barthel focused on reducing binding weight by using the boot itself to eliminate the frame of existing touring bindings. “I locked myself up in our basement—there was and still is a little workshop—and started thinking about it, trying, playing,” Barthel says in Dynafit’s Low Tech’s 30th Anniversary book. “I needed to create a strong enough interface in the tip of the boot to hold the pins of the front piece of the binding.”
Barthel was studying in Graz, Austria, where Dynafit, one of the few touring boot manufacturers at the time, was based. After experimenting with some donated shells, he realized only a fitting molded into the boot could withstand the forces of ski touring. His father, who admittedly had a personal motive to speed up his own touring, donated the funds to modify the molds for the inserts.
In 1984 Barthel was awarded his first patent and presented his prototype to most of the larger boot and binding manufacturers—and the rejection letters rolled in. As a result, Barthel started manufacturing the bindings by hand in his basement. He sold 10 pairs that first year, coupled with specially molded Dynafit boots that he purchased to sell as a set.
About the name, Barthel explains in the anniversary book, “At the time, everything had to be called ‘high-tech’ to be successful. But, what should this lightweight, mechanically simple binding be called? Low Tech, of course.”
By 1990, he was selling a 1,000 pairs, still out of his house: “Imagine 1,000 ski-boot boxes in a house—boxes from the basement to the attic, everywhere.” That same year, Dynafit took over production of the binding, changing the name to Tour Lite Tech. Barthel then began consulting with Dynafit and still does today.
The binding first gained interest and then acceptance with randonnée rally racers, with the Italians becoming the largest converts. In those days, the team-based races were held in stages over multiple days, with penalty points assigned for stages not completed in the allotted time and requiring nights spent out in self-constructed igloos.
The binding evolved quickly from the earliest prototypes. By 1986, it had become easily recognizable as the tech ancestor. The 1992 version showed off the flashiest early ’90s neon—pink, green and purple. In the ’94 model, the heelpiece replaced the swappable U-spring with an adjustable vertical release. Brakes were an option for the first time in 1996.
In 2005, the line forked into ski touring and more race-oriented branches. The following year saw the beginning of the Vertical, Radical and Radical 2.0 lineage that has culminated with today’s Rotation. The rotating toe of the 2.0 and Rotation formed a key component necessary for TÜV safety certification—the standard per the International Organization for Standardization (ISO) 13992—for touring bindings. Dynafit’s racing branch brought the U-spring back into play with superlight heelpieces. Currently, the P49 race binding, weighing 49 grams per side, flips things around and puts the spring-loaded pins in the boot and the pockets in the rigid toe wings.
Over the past 36 years, nearly 40 models and variations have evolved from Barthel’s original idea. In fact, the only constant may be Barthel himself—his photos from 1989 and 2013 in Low Tech’s 30th Anniversary look exactly the same.
Related posts:
The Human-Powered Evolution of Greg Hill
Backcountry Access: Leading safety technology, 25 years later
25th Anniversary Editor's Note: Tripping Forward
25th Anniversary Editor's Note: Townie Talk