Both ski design and construction are evolving rapidly and constantly. To get a glimpse into the latest thought processes, I interviewed two companies on the leading edge.
DPS is overhauling their carbon skis with the new Alchemist line—that’s touted as having more damping qualities than their previous Pure3 construction—and Black Crows continues to improve and lighten their tester-loved Freebird skis. And both companies are guided by passionate skiers making developments for the future of backcountry skis.
To learn more, I asked Black Crows designer Julien Regnier and Kenji Teshima, their product development manager, just how they work together to develop a new ski. I also chatted with DPS founder Stephan Drake and Peter Turner, their director of engineering, about how they blend their backgrounds and skills to produce a new ski. Here’s what they all had to say.
Anna Riek: Who typically originates the concept for a new ski?
Black Crows’ Julien Regnier: I look at what I need and sometimes at what other riders on the team want, and we make ourselves skis. Yes, it is a bit ironic but kinda true. Our brand is very much driven by skiers from big mountains, to recreational groomer skiing, to steep, scary skiing. We love all kinds of sliding processes, and I’m here to give a shape answer. Our skis are always an answer to a demand of a skier.
AR: Describe how you and Kenji Teshima work together to develop a new ski.
Regnier: We discuss what the product should be about and that’s a five to six [person] discussion. Then we test other products to see what we are up against and to get a good feeling of what we want. Then, I draw the ski. Three people usually overview it. We start talking with our factory for flex reference and general dialogue about the ski. The first proto comes out, and if the ski is working, we start optimizing the flex until we’re satisfied with the performance.
AR: What makes an ideal touring ski and how do you develop it?
DPS’s Peter Turner: We research appropriate materials and construction options while defining the ski geometry. Trials are made with those development materials until we arrive at the solution that meets our goals.
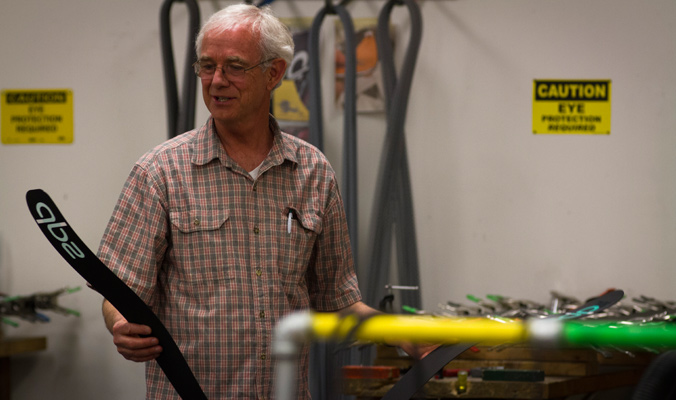
Turner covers his bases. [Photo] Dan Pizza
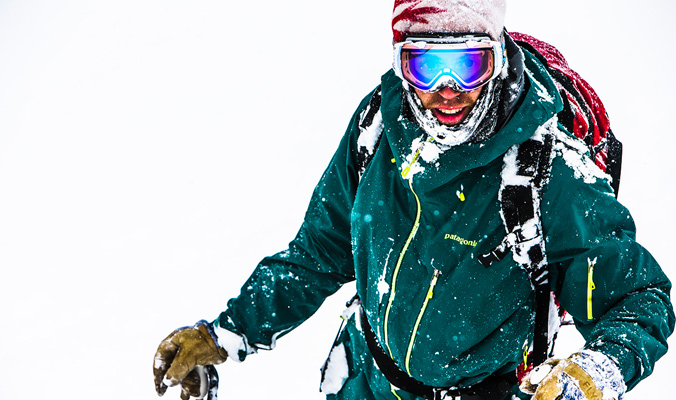
Stephan Drake tests his products. [Photo] Oskar Enander/DPS
AR: Do new materials and construction drive the design? Or does the design concept search out new materials and construction?
Drake: It’s a combination of both. Tour1 construction was developed to meet weight goals. A more lightweight touring ski requires cap construction [to] eliminate the weight of sidewalls, and a lightweight core and high performance laminates to make up for the lighter core, as an example. For Tour1, we created a custom laminate architecture with new carbon materials never used before in skis. We had previously played with this laminate as a candidate for the Foundation line, but it happened to work quite well with Tour1. And so it stuck and ended up as a net improvement to Tour1’s weight and performance.
Regnier: We do a lot of testing for new materials and we are open for any new idea, but I do place the shape at the center of all development; the rest is optimization. You can make a great ski with carbon going through it, and you can also make an equally good ski without the carbon. Optimization of your basic idea—that’s the strength, the product. The rest is marketing. We do spend a lot of time thinking and testing our product. We work with basic technologies and put [in] extra effort to make it ski very smoothly.
AR: How do you approach the design of your Freebird skis versus the All Terrain/Big Mountain models?
Regnier: Freebirds are made to be skied with touring gear, so this is a big point of difference. The sidecut on certain models is also different, even for a ski that has the same width, because the practice is a little different. I talk to people a lot and try to understand how they ski our skis.
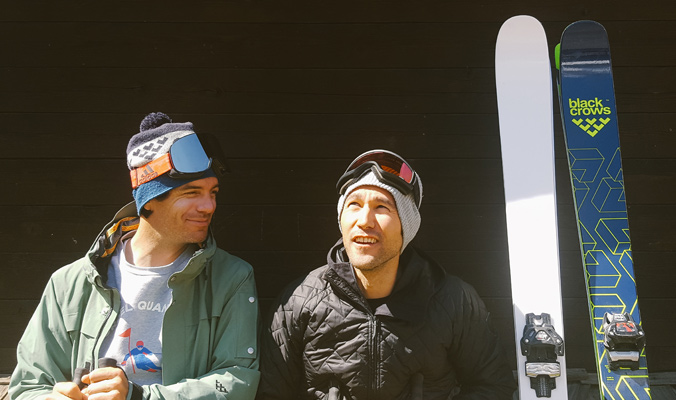
Julien Regnier (left) and Kenji Teshima (right) talk ski construction. [Photo] Courtesy Black Crows
Drake: Tour1s are driven by weight as a dominant design component. In the Alchemist, superior alpine performance coupled and complemented by light weight is the goal. Thereby, materials and construction approach vary accordingly. Each construction reflects the dominant design intent in terms of core choice, laminate choice, damping agents, etc. Foundation is a bit of a different animal in that lightweight takes a backseat to damping and the feel of a more traditional fiberglass ski, so you get bamboo underfoot, triaxial fiberglass and carbon stringers as opposed to a full carbon laminate. Foundation skis are still typically 10- to 15-percent lighter than competitive glass skis in the same categories.
AR: What is the biggest challenge to designing touring skis?
Drake: Finding that perfect blend of performance, weight and durability. When you make things lighter, you are invariably fighting reduced damping performance and potentially durability concerns. The question becomes how far to push each of these characteristics and still come up with a great blend of characteristics.
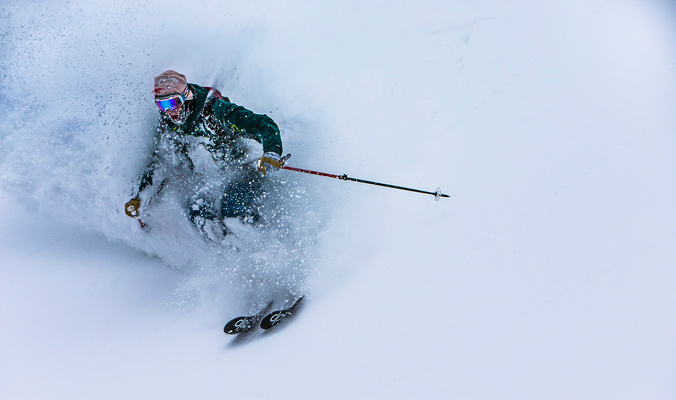
Stephan Drake sees if he has found the right blend. [Photo] Oskar Enander/DPS
Turner: We are looking at new materials and refinement of existing ones to improve all of the desired attributes.
Regnier: A heavy ski skis very well—keep that in mind. Unless you are a ski alpinist runner, which is not our market right now, you just want a well-balanced ski; and, we will keep testing and optimizing our skis to fulfill that goal.
AR: Is there anything you would like to add?
Drake: Design and engineering are at the core of our identity. For us, skis aren’t fashion; they are special technical tools, and we have always been committed to pushing the best, most innovative materials possible while mating them with sound design.
Regnier: I would love to have an automatic skin roller on my skis—I would probably place it on the tail.
Teshima: E-skins will come soon in the touring market.
Related posts: